Connect with ASBI
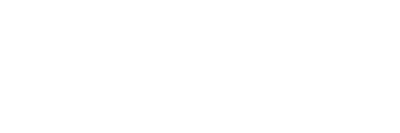
9901 Brodie Lane, Suite 160 PMB 516 • Austin, TX 78748
Phone: 512.523.8214
Copyright © 2023 American Segmental Bridge Institute
The existing Ironton-Russell Bridge, a cantilever structure, was opened in 1922 as the first highway bridge along the Ohio River between Parkersburg and Cincinnati. It was retrofitted in the 1970s and later posted with restrictions, having become inefficient for traffic and economically impractical to maintain. In 2000, the Ohio Department of Transportation (ODOT) determined the bridge was functionally obsolete and structurally deficient, and recommended a full replacement.
Unlike the original bridge, which connects downtown Ironton with downtown Russell, the new bridge connects downtown Ironton directly with US 23 and KY 244 within the city limits of Russell just south of downtown. This bridge is a major river crossing that provides a main route for trucking and transportation for Ohio. The new bridge opened on Wednesday, November 23, 2016, with a ceremony and parade through Ironton and Russell that included crossing both the new and original structures.
Innovation of Design and/or Construction
The new 2,616-ft.-long Oakley C. Collins Memorial Bridge is comprised of a 900-ft. cable-stayed main span and two 370-ft. cable-stayed side spans, two 326-ft. tall towers and two anchor piers on the river’s edge. The structure is cast-in-place with 22,500 cy of reinforced concrete (5.8 million lbs. of rebar), utilizing the cable stays to construct the bridge by the one-directional cantilever method. Foundation units consist of 22 large, 96-inch diameter drilled shafts.
The 900-ft. main span is the longest span ODOT has ever built. Construction began in March 2012 and was completed November 2016.
There were several key modifications to the means and methods and design optimizations, most notably:
Minimizing Water-Based Work – During the pre-bid phase, the Team wanted to minimize water-based work since this adds substantially to cost, schedule and safety risk, especially since the river can rise over 20 ft. in this area.
Constructing the back spans on falsework simplified construction, reduced construction time, increased project safety, and reduced the amount and size of equipment required for the cable-stayed portion of the project. The falsework was designed as a modular system, allowing it to be used for both the Kentucky and Ohio approaches and reducing the number of travelers from two to one. This, along with precast concrete girders for floor beams on side spans, allowed the Contractor to have land access to build the main span area.
These modifications to the construction sequencing saved costs and time, as well as providing a much safer work environment. Project officials concur that minimizing water work was a wonderful success. With an average of 50 workers on-site, on a daily basis, there was no lost time incidents on this project.
Precast Where Possible – The Team evaluated and identified elements that could be precast rather than poured in place, allowing items to be pre-manufactured under controlled conditions, while other work was able to continue. The use of precast cofferdams greatly reduced the amount of tremie concrete required, as well as provided a sacrificial form for the tower footing.
Precast tubs were used for footings at Pier 3 and Pier 4, eliminating the need for pile coffer cells, effecting schedule and cost savings. The precast tubs were tied into the drilled shafts, reducing its footprint, minimizing excavation and its impact on the environment, footing form costs and schedule time. In addition, floor beams were precast and stay-in-place deck forms were used on the side spans.
Precast Stay Anchor Block System – The design of an innovative precast stay anchor block system simplified stay cable anchorage placement, accelerated the construction schedule and simplified the form traveler system by eliminating the need for a temporary stay anchorage.
Rapid Construction
While the original design specified the use of two form travelers, the modifications allowed the main span to be cast-in-place in a segmental, one-directional cantilever method. It allowed the integration of the design and fabrication of the traveler through one stay supply and installation provider.
The cost was $655 per square foot. The design optimization and changes to the construction method resulted in a winning bid approximately 4% below the state’s final estimate of $84.6 million.
Aesthetics and/or Harmony with the Environment
The grand opening ceremony of the new Oakley C. Collins Memorial Bridge took place on November 23, 2016, in Ironton, Ohio, and hundreds of people turned out for the opening ceremony. A parade featured classic cars and local groups, including the Russell and Ironton High School bands.
The bridge creates a safer route for the traveling public, as well as a safer route for the navigational channel.
The iconic cable-stay bridge is a type popular for the past couple of decades for its combination of aesthetic good looks, projected long life span, and low-maintenance cost.
Minimization of Construction Impact on the Traveling Public
The original bridge remained open during construction until the new bridge was completed. The innovative and first use of a precast stay anchor block system in the United States simplified stay cable anchorage placement, accelerated the construction schedule and simplified the form traveler system by eliminating the need for a temporary stay anchorage.
Jury Comments
This project demonstrated how segmental concrete provides multiple options to a designer and contractor to design and construct a long-span bridge fast and economically. ODOT’s longest span bridge is an amazing technical and aesthetic achievement. Use of precast stay blocks and backspan falsework was innovative and saved substantial construction time.
2017 ASBI Award of Excellence
Category: Long-Span and Cable-Stayed Bridges
States:
Ohio/Kentucky
Owner:
Ohio Department of Transportation
Owner’s Engineers:
AECOM
Designer:
AECOM
Contractor:
Brayman Construction Corporation
Construction Engineering Services:
Finley Engineering Group, Inc.
Construction Engineering Inspection:
FIGG
Precast Producer:
Carr Concrete/Brayman Precast LLC
Form Travelers for Cast-in-Place Segments:
Structural Technologies VSL
Formwork Tower Leg Forms:
PERI Formwork Systems, Inc.
Post-Tensioning Supplier:
Structural Technologies VSL
Stay Cable Materials:
Structural Technologies VSL
Bearings:
D.S. Brown Company
Expansion Joints:
Watson Bowman Acme
Epoxy Supplier:
Pilgrim Permocoat, Inc.
Prepackaged Grout:
The Euclid Chemical Company