Connect with ASBI
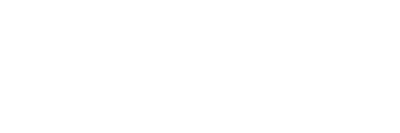
9901 Brodie Lane, Suite 160 PMB 516 • Austin, TX 78748
Phone: 512.523.8214
Copyright © 2023 American Segmental Bridge Institute
The new South Norfolk Jordan Bridge linking Chesapeake and Portsmouth, Virginia opened to traffic in October 2012, providing faster connections, more capacity, bigger clearances, and breathtaking views to enhance the quality of daily life in surrounding communities. This new, modern concrete segmental bridge was built in less than 2 years to replace a structurally deficient steel lift span bridge that was closed to traffic. Since there was no funding available to repair or replace the aging bridge, the City of Chesapeake had no choice but to close it to traffic, resulting in greater congestion on routes many miles away. The new segmental bridge was accomplished using 100% private funds.
Precast segmental technology was used to construct both the full super-structure and substructure of the new bridge. Each element of the bridge, the foundations, piers, and superstructure were manufactured in local precasting facilities and then assembled on-site. Precasting offered many benefits including speed of construction, multiple construction headings, and factory-like quality control. Precast balanced cantilever construction accomplished the long (385′) span over the river’s navigation channel. Typical spans (150′ long) were built using span-by-span construction with segments delivered over previously completed portions of the bridge. The final bridge layout is 5,375 feet long, with a total of 35 spans. The bridge segmental approaches consist of typical spans that are 150′ long.
Innovation of Design and/or Construction
After extensive analysis, engineers achieved a bridge layout that provides the required navigation clearance of 145′ (vertical) and 270′ (horizontal), gentle grades for pedestrian access, appropriate rail clearances, while also integrating the bridge seamlessly into the existing transportation network including I-464.
Bridge foundations consist of 24″ square prestressed concrete piles for land piers, 54″ diameter prestressed concrete hollow cylinder piles for piers in the water, and 66″ diameter concrete cylinder piles for the bridge fender system. Engineers selected pile foundations with above ground footings to avoid excavation of potentially contaminated soil in an existing superfund site along the west bank of the river.
Each of the concrete box segments for the columns were precast adjacent to the bridge site. The column segments were cast in two precasting beds using self-consolidating concrete with a compressive strength of 5,500 psi. The precast box column segments were stacked in place and then post-tensioned to build piers ranging in height from 18′-9″ to 144′-10″ tall at the main span.
The bridge’s superstructure consists of both constant depth segments for the 32 approach spans and variable depth segments for the main span unit that range from 9′-2″ at mid-span to 18′-5″ at piers. All of the segments are 51′-8″ wide to accommodate the bridge’s two 12′ travel lanes, two 8′ shoulders, and an 8′ barrier protected pedestrian sidewalk. Superstructure segments also include a 1.5″ integral concrete wearing surface for enhanced durability. Concrete compressive strengths of 6,000 psi and 8,000 psi were specified by design with well over that strength achieved for the produced precast superstructure segments.
Span-by-span construction with twin underslung trusses was used to build each of the 32 approach spans. Segments were delivered over the completed bridge, loaded onto the truss, and then post-tensioned together. The bridge’s smallest horizontal curve radius of 750′ was achieved with span-by-span construction and underslung twin temporary triangular trusses.
The main span unit over the river was built using balanced cantilever construction which required close coordination with the United States Coast Guard to keep vessels in the channel moving, including the nearby Norfolk Naval Shipyard. Segments were barged to the bridge site and then lifted into place.
Rapid Construction
Total construction time on the South Norfolk Jordan Bridge was less than two years, minimizing the construction and environmental impact, traffic and noise. Precasting of the bridge elements allowed for construction of the piers, approach spans, and main spans simultaneously. Pier erection started on the west end of the bridge while superstructure segments were continuing to be cast, working toward the east. To allow for delivery of precast segments, approach span construction also proceeded from west to east, following pier erection. At peak production, crews achieved two approach spans per week and erected six variable depth main span segments per day.
Aesthetics and/or Harmony with the Environment
The curves of the segmental bridge create interesting and unexpected views from underneath and atop the structure. Landscaped areas along the bridge approaches and park areas with new amenities provide a gateway to the area and new gathering areas for the community to enjoy. Additional areas are now accessible to the public as the new bridge gracefully soars over the expanded Elizabeth River Park and Boat Launch under the bridge in Chesapeake. Pedestrians can walk to the top of the bridge for a spectacular bird’s eye view of their community and the entire surrounding Hampton Roads region, including distant views of Norfolk and Virginia Beach.
One of the most innovative aspects of the new bridge is the emphasis on environmental responsibility:
Cost Competitiveness
Through the use of innovative partnerships this new bridge was accomplished with 100% private funds. The bridge is privately owned, operated and maintained, and supported through user fees (tolls). This innovative arrangement is an example for future efforts in replacing the country’s deficient bridges quickly and cost-effectively using precast concrete segmental technology.
Jury Comments
Bridge leverages segmental construction for both the superstructure and substructure to complete the 17-story, one mile long structure in two years – outstanding!
2013 ASBI Bridge Award of Excellence
Category: Bridges Over Water
State:
Virginia
Owner:
United Bridge Partners
Designer:
FIGG
Owner’s Engineer:
FIGG Bridge Builders
Contractor:
FIGG Bridge Builders and Lane Construction
Construction Engineering Inspection:
FIGG Bridge Builders
Precast Producer:
Atlantic Metrocast
Formwork for Precast Segments:
Southern Forms, Inc.
Post-Tensioning Materials:
VSL
Bearings:
D.S. Brown Company
Expansion Joints:
D.S. Brown Company
Epoxy Supplier:
Pilgrim
Prepackaged Grout:
Euclid